Field and Supply Use
Field and Supply Use
Difline products and their applications
Diflon’s standard delivery program includes PTFE-lined carbon steel tubes and fittings in various versions from the DN 15 to the DN 600, for standard tube lengths up to 3 m and extended tube lengths up to 6 m. The continuous application temperature ranges from –29°C to +260°C, however, under certain conditions, these limits can be exceeded for a short time. In the standard versions (PN10/16 – ANSI 150) and at ambient temperature, the Difline products can be used in applications not exceeding 13 bar. For higher pressure values, tubes and fittings in the PN 25 and PN 40 versions are available on request. All Difline installation components feature high resistance against vacuum conditions. For absolute vacuum applications, the special versions HD (see table 1). The extraordinary properties of the PTFE material used by Diflon allow the application of Difline installation components on virtually all fluid media. The material’s properties are particularly appreciated in the handling of highly aggressive media such as hydrochloric, hydrofluoric and nitric acids, oleum (fuming sulphuric acid), etc. On the contrary, PTFE is not recommended with alkali metals, chlorotrifluoride and elemental fluorine (at high temperature and pressure).
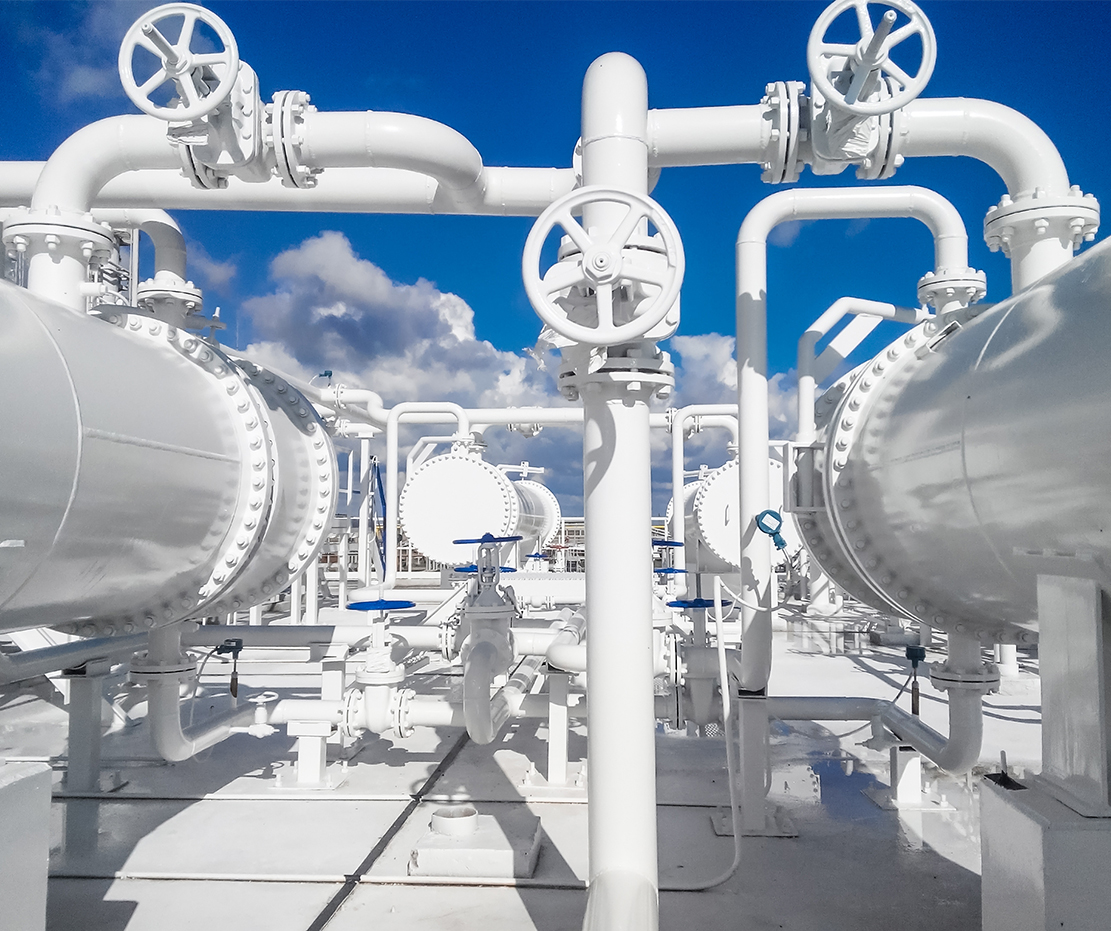
Quality
Quality, Test and Certifications
Quality, Test and Certifications
Non-destructive tests carried out on Diflon engineering products include:
- Poroscope from 5000 to 50000 V
- Hydraulic test up to 80 bar
- Non-destructive tests: radiographs, penitent liquids, magnetoscopic control - SMEs
- Ferroxyl test
- Other tests on request
Quality control of manufactured goods and certificates
• physical properties of PTFE
• physical and chemical properties of steel
• dimensional check of items
• check of machining tolerances
• simulation of the expected application limits.
• other tests on request
Finishing, Branding and Packing
Finishing, Branding and Packing
Final treatment of surfaces and painting
Steel surfaces are normally finished by brushing, and by applying an epoxy-based rust proofing paint:
• sandblasting to SA2 1/2 grade
• application of one or two coats of an epoxy enamel in the required color
application of zinc-rich paints can be additionally carried out.
Protection for handling and storage
All Diflon items are provided by suitable protections, such as plastic or special cardboard caps on the stub ends at the flanges, to protect them from damage during transportation, handling and throughout the storage period, until they are used. Protections shall be removed only immediately before installation and assembly with the other components. The accidental damage, due to impact, of the sealing face of the flange can seriously impair the entire item.
Assembly and set up of equipment, steel pipes and fittings PTFE lined steel
No particular tool is required to assemble PTFE-lined pipes manufactured by Diflon; nevertheless, some basic rules should be complied with for the optimum performance of all components.
•A thorough on-site survey should be carried out to determine the size and dimensions of the piping to be installed; this is in order to avoid post-installation adjustments and makeshift solutions unsuitable for the intended service.
•Whenever possible, standard items should be used in order to facilitate eventual replacement.
•Adjustable sleepers and supports should be foreseen to avoid any strain in pipes due to inaccuracy and imperfect alignment of supports during assembly and operation.
•Pipes should not be forced when adjusting them, an unstable sealing of the flanged couplings only could be achieved. Should any adjustment be required, shimming rings or solid PTFE shimming units must be employed.
•In order to avoid permanent damage, PTFE-lined steel components should not be welded according to the conventional procedure.
•No sealing compound or adhesive putty should be inserted between the flanges; it could impair their tightness and integrity.
•The use of a torque wrench is recommended for flanged couplings; a tightening pressure will be achieved that is evenly distributed throughout the sealing surface.
•The use of Diflex gaskets is recommended on couplings in order to protect stub ends from incorrect tightening.
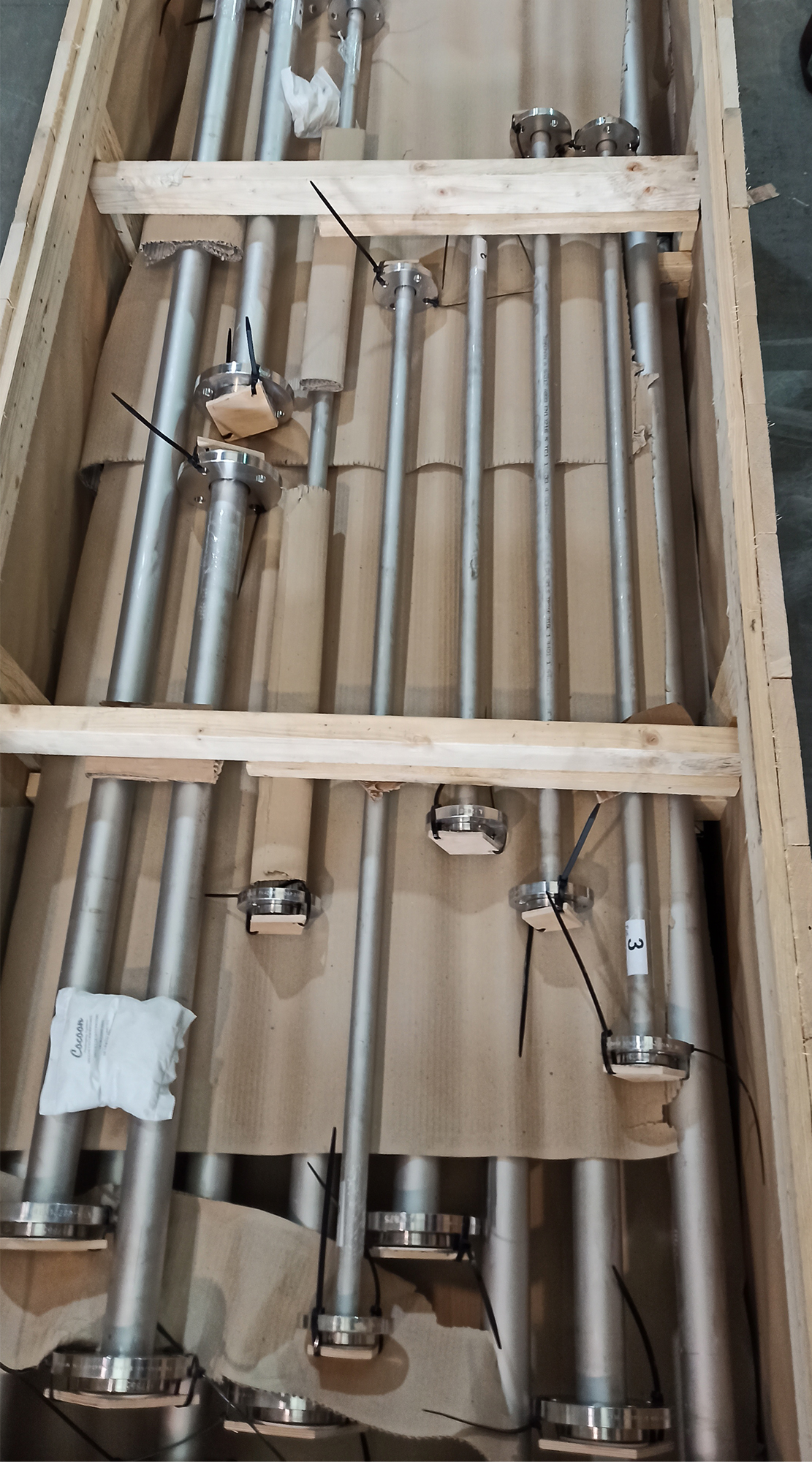
PTFE
PTFE Properties
1. PTFE FEATURES
Polytetrafluoroethylene (PTFE) is a tetrafluoroethylene polymer featuring a unique combination of physical-chemical features that make it different from any other plastic material. The main features of PTFE are: • extreme chemical inertness
• excellent heat resistance
• optimum dielectric properties
• zero hygroscopicity and maximum resistance against solvents
• optimum resistance to ageing
• self-lubricating properties and minimum friction coefficient.
CHEMICAL PROPERTIES
PTFE withstands virtually all chemical reactants. It is only attacked by elemental alkali metals, chlorotrifluorides and elemental fluorine at high pressure and high temperature. PTFE is indifferent to all solvents up to 300°C. It can only be swelled and melt by some highly fluorinated oils at temperatures around the crystalline melting point.
THERMAL PROPERTIES
PTFE has a low heat transmission factor and can be therefore considered a thermoinsulating material. It also shows flame- retardant properties and is stable at 260°C for an indefinite length of time.
ELECTRICAL PROPERTIES
PTFE has optimum dielectric properties within a vast range of temperatures and frequencies. As water absorption is virtually inexistent, these properties are maintained even after a prolonged exposure to weather agents. Electric strength is practically not influenced by the operating temperature. The resistance to arcing of PTFE is considerable and the spark does not generate carbon residues but only non-conductive vapours.
The other electric properties (dielectric constant, surface resistivity, volume resistivity, power factor, etc.) show very interesting values.
MECHANICAL PROPERTIES
The following table displays the mechanical properties of PTFE, measured at the temperature of 23°C. Take note that between 19°C and 21°C, the material shows a transition point determined by a modification of its crystalline structure which provokes a loss of volume of about 1%. Other particular properties of PTFE are its non-adhesivity and its low friction coefficient, above all under high loads.
PTFE technical specifications
Properties |
Method |
Unit of measure |
Values |
Specific gravity |
ISO 1183 |
- |
2,130 - 2,180 |
Tensile strengthe |
ISO 527 |
MPa |
20 - 30 |
Elongation |
ISO 527 |
% |
200 - 350 |
Hardness |
ISO 868 |
Shore D |
54 - 60 |
Elasticity module |
23°C |
N/mm2 |
600 - 700 |
Deformation under load (140 kg/cm2 for 24 hrs at 23°C) |
ASTM D695 |
% |
10 - 13 |
Permanent deformation (after 24 hrs - Relaxation at 23°C) |
ASTM D695 |
% |
6 - 7,5 |
Friction coefficient |
ASTM D1894 |
/ |
Dynamic 0,07 |
Dielectric constant at 60 Hz to 2GHz |
ASTM D150 |
/ |
2,1 |
Dielectric strength |
ASTM D149 |
kV/mm |
20 -70 |
Volume resistivity |
ASTM D275 |
Ohm cm |
1018 |
Flammability |
UL 94 |
% |
VE-0 |
Melting point |
|
°C |
325 - 335 |
Water absorption |
ASTM D570 |
% |
0,01 |
Antistatic PTFE 1,2% CSC technical specifications
Properties |
Method |
Unit of measure |
Values |
Specific gravity |
ASTM D792 |
g/cm 3 |
2,140 – 2,170 |
Tensile strength |
ASTM D4894 |
MPa |
> 22 |
Elongation |
ASTM D4894 |
% |
> 250 |
Hardness |
ASTM D2240 |
Shore D |
> 60 |
Coefficient of static friction |
ASTM D1894 |
|
0,08 – 0,10 |
Coefficient of dynamic friction |
ASTM D1894 |
|
0,06 – 0,08 |
Volume resistivity |
ASTM D257 |
Ohm cm |
104 |
Surface resistance |
ASTM D257 |
Ohm |
103 |
Ageing and weatherability |
|
Stable over 20 years of exposure |
Service Temperature |
|
C° |
-200/ +260 |
PFA
PFA Properties
PFA PROPERTIES
PerFluoroAlkoxy alkanes (PFA) is a fluoroplastic. It is produced by copolymerization of tetraefluoroethylene (C2F4) and perfluoroethers (CF2F3ORf). In terms of its properties, this polymer is similar to polytetrafluoroethylene (PTFE). The big difference is that the alkoxy substituents allow the polymer to be melt-processed. PFA is melt-processable by conventional thermoplastic processing methods, including injection, transfer, blow, and compression molding and by extrusion. It is a relatively soft thermoplastic with lower tensile strength and creep resistance than many other engineering plastics. It is chemically inert and has a low dielectric constant over a wide frequency range. PFA is used when extended service is required in hostile environments involving chemical, thermal, and mechanical stress. PFA offers high melt strength, stability at high processing temperatures, excellent crack and stress resistance, a low coefficient of friction.
It has high resistance to creep and retention of properties after service at 260°C (500°F). PFA also meets FDA 21CFR.177.1550. PFA has high transparency (with good transmittance of UltraViolet and visible wavelengths.) It has long term weatherability and excellent resistance to ozone, sunlight and weather. Important applications are linings for pipe and chemical processing equipment, roll covers, and several wire and cable applications, including aircraft wire, plenum cable, fire alarm cable, and well logging cable.
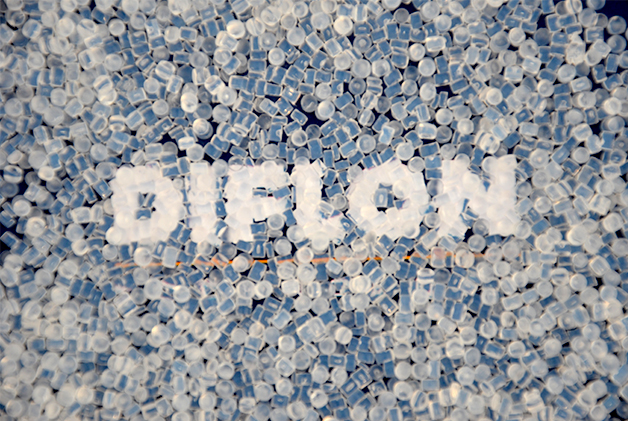
PFA SPECIAL FEATURES
• Wide service temperature range
• Extremely high weathering resistance and UV stability
• High limiting oxygen index: Does not support combustion
• Good non-stick characteristics
• Broad processing window
• Improved mould release property
• High transparency
• Excellent, almost universal resistance to solvents and chemicals
• Excellent electrical insulation properties, e.g.: dielectric breakdown strength, dielectric constant • Smooth surfaces
• Good low-friction properties
• Improved stress crack resistance Properties
ANTISTATIC PFA Technical specifications
Fluoroplastic PFA is an electrostatic dissipative fluorothermoplastic compound consisting of a fully fluorinated PFA base polymer and an electroconductive carbon black. The product has specifically been developed for transfer moulding.
ANTISTATIC PFA Special Features
- Electrostatic dissipative
- Processing: Transfer moulding
- Wide service temperature range up to 240 °C Properties Test method Unit Value*
Typical Properties
Fluoroplastic PFA compound that is electrostatically dissipative. Typical Applications
Typical Applications
Fluoroplastic PFA, is a material with a high viscosity and is used in low shear processes. Fluoroplastic PFA has specifically been developed for transfermoulding , when an electrostatically dissipative product is required.
PFA Technical specifications – Perfluoroalkoxy
Property |
Method |
Units |
Specification |
Specific Gravity |
DIN EN ISO 12086 |
g/cm3 |
2.15 |
Melting Point |
DIN EN ISO 12086 |
°C |
308 |
Melt Flow Index (372 °C/5 kg) |
DIN EN ISO 1133 |
g/10 min |
2 |
Limiting Oxygen Index (LOI) |
ASTM D2863 |
% |
> 95 |
Hardness Shore D |
ASTM D2240/ISO 868 |
- |
60 |
Tensile Strength at Break (23 °C) |
ASTM D638 |
MPa |
34 |
Elongation at Break (23 °C) |
DIN EN ISO 527-1 |
% |
360 |
Flexural Modulus |
DIN EN ISO 527-1 |
MPa |
550 |
MIT Folding Endurance (200 μm film) |
ASTM D 2176 |
double folds |
3.1 Mio. |
Specifiche tecniche PFA ANTISTATICO
Property |
Method |
Units |
Specification |
Specific Gravity |
DIN EN ISO 12086 |
g/cm3 |
2.11 |
Melting Point |
DIN EN ISO 12086 |
°C |
278 |
Melt Flow Index (372 °C/5 kg) |
DIN EN ISO 1133 |
g/10 min |
2 |
Tensile Strength at Break (23 °C) |
ASTM D638 |
MPa |
30 |
Elongation at Break (23 °C) |
DIN EN ISO 527-1 |
% |
290 |
Volume Resistivity |
DIN ICE93 |
Ohm x cm |
<10.000 |
Quality and Special Tests
Quality and Special Tests
Tests
• Hydraulic
• Pneumatic
• Scintigraphy
• Visual / Dimensional
• Thickness
• X ray (with film viewer)
• Magnetic particle
• Penetrating fluids
• PMI (stainless steel only)
• Passtivation (stainless steel only)
• Holiday test over coating
• Dry Film Thickness
Engineering Services
Engineering Services
Engineering Services
We carry out detailed engineering services, with technical drawings and lists of materials for the various implants, which occur to the use of fluoropolymer and steel materials. We perform measurement and design services from the preliminary system to the final supply, with a list of materials and related chemical implants, with CE certifications. We supply complete valve packages. At our factory in Carobbio degli Angeli we develop the engineering projects, we carry out the processing of coatings, and we produce tanks and columns in fluoropolymers and steel, designed with 3D technologyand tested according to CE and PED certifications. We offer the production of flexible pipes for the industry where you can request characteristics and dimensions. We can also develop, with an exclusive engineering service, metal bodies to be prepared for coating with fluoropolymers and polypropylene. In addition, we make molded cast and lost wax parts with tolerances of 00. For carbon steel the tolerance is: 00. We are strongly encouraged to accept cost and engineering challenges that concern fluoropolymer and polypropylene coatings of metal parts. The cost of the engineering service is 50 euros / hour and the cost of mergersit is about 3.5 for the lost wax with a tolerance of: 00. We can tackle every problem with professional experience. Our services offer the best quality at affordable prices.
• Surveys directly on the spots
• Detailed engineering
• Stress Analysis
• Assistence while assembling
• Developing of itemized lists
• Stirrups design
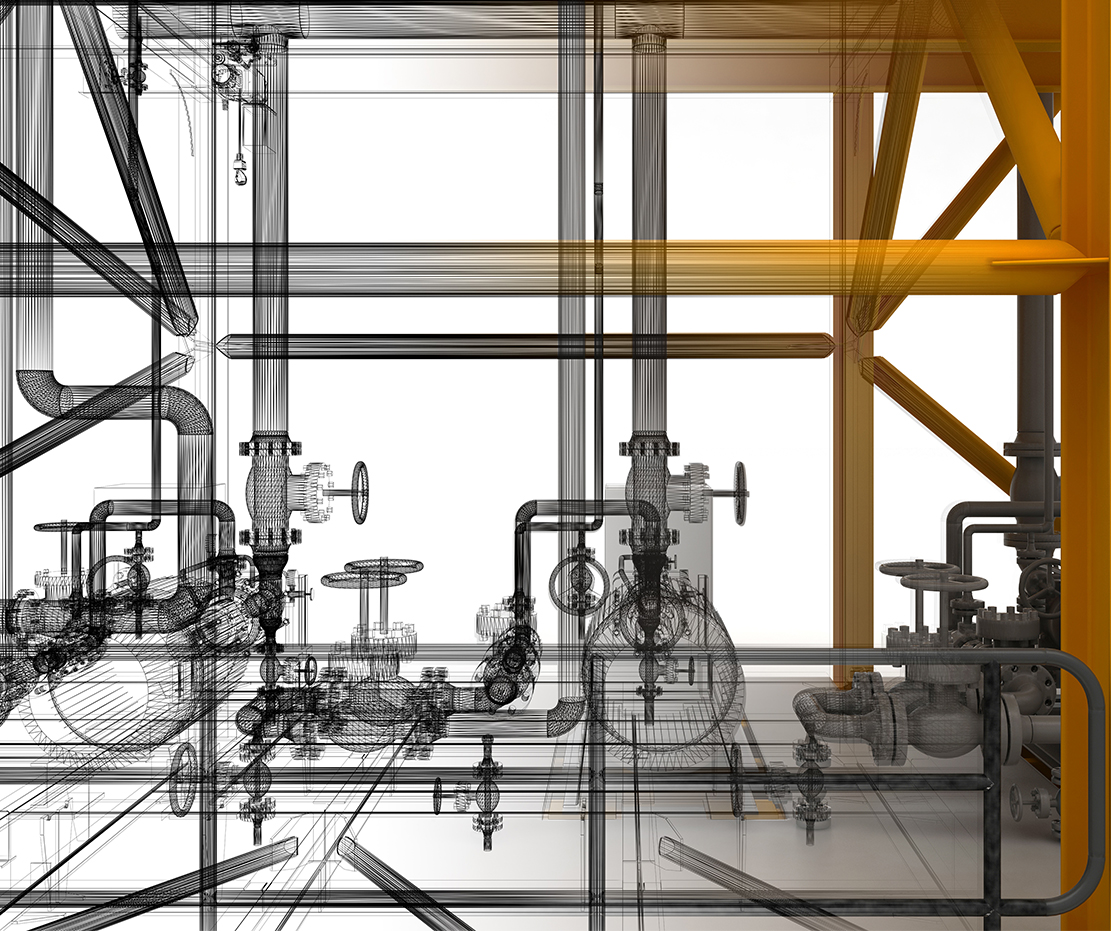
Special Supplies
Special Supplies
Surfaces Finishing
Surfaces Finishing